Injured workers, jobsite delays and shutdowns, hefty OSHA fines – these are just a few of the problems that can eat away at heavy civil companies that don’t have a firm grasp on their overall safety culture. However, implementing a reputable safety program can alleviate these problems. In fact, one HCSS customer lowered their EMR by 0.15 in only one year.
Offering some advice is an industry expert who helps businesses tackle this daunting task with measurable results!
Meet Hope
Hope Matheny is a Certified Safety Professional and Environmental Manager with over 25 years of experience in the construction industry. She’s also the founder of HLM Safety and Environmental Services, a launchpad for helping fellow construction companies develop and fine-tune their safety programs.
“First and foremost on our agenda, on a daily basis, is staying safe,” Matheny states. “When we don’t have a good plan that incorporates a safe environment, workers are not focused on production.”
“First and foremost on our agenda, on a daily basis, is staying safe. When we don’t have a good plan that incorporates a safe environment, workers are not focused on production.”
– Hope Matheny, Founder, HLM Safety and Environmental Services
For Matheny, one of the biggest struggles she’s seen organizations face in the field prior to incorporating a software program is doing great training on one project where workers were properly equipped, and then moving on to another project and not having the training documents.
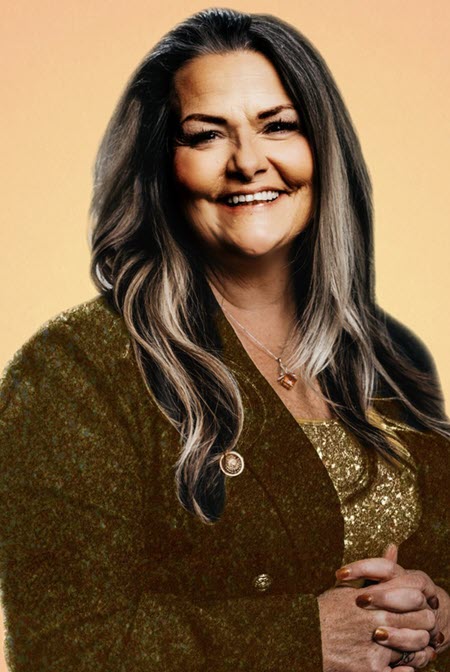
“You want to talk about a slowdown in productivity?” Matheny says. “We would have to redo all this training that we had very recently just done because we didn’t have the documentation. It’s such a money-saver if you can be organized from a technology standpoint to access that stuff right away.”
Another frustrating problem with this is hurting employee morale. People who work in construction and love it are naturally competitive, and they like to be on the move, getting jobs done. When you’re being held up because of a paper issue, it whittles away on that trust. If you’re just trying to meet compliance, not trying to be safe, then you’re wasting your time.
Affecting Employee Engagement for the Better
From a reputation standpoint, a lot of times as safety professionals, we fall short of expressing to our insurance carriers – who are evaluating our processes and how we handle risk – where we really do shine in our programs.
“Inherently, I can say from an owner’s perspective, if you’re not leveraging a software to really analyze what’s going on on the project, you are missing an opportunity,” says Matheny. “I have been in the seat myself where we’re trying to prevent employee injury or property loss in the field, and we’re doing everything possible that comes to mind to try to minimize that risk and repeated injuries. But to be quite honest, if we’re still at the compliance level where we’re just expecting employees to fill out documents that are heading to the box, we’ll never be able to leverage ourselves to the next level to really get a handle on what risks our employees are up against and how we can leverage our software and our programs to reduce that risk.”
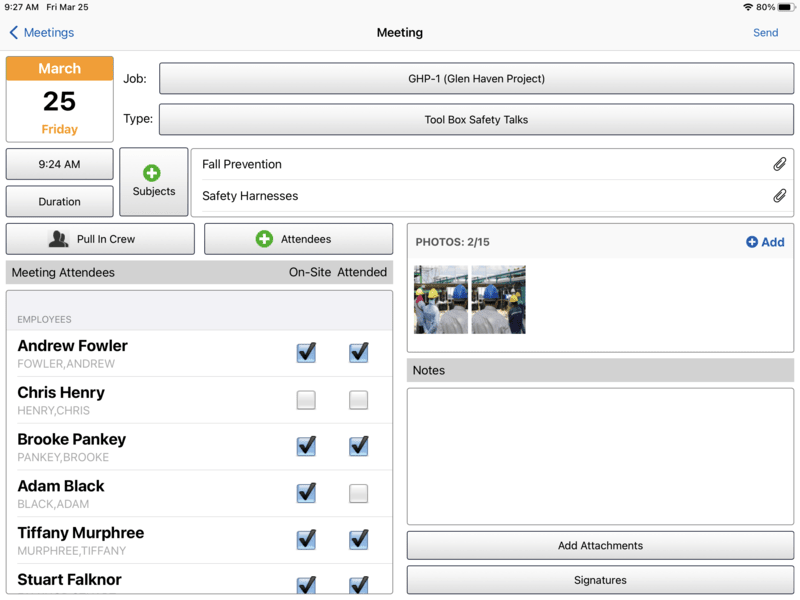
It’s important to fully understand what kind of risk workers are up against every day across an organization. Unless you’re a worker, you really don’t know. That said, if you don’t have a good safety reputation in the industry, you will not win consistently. Those workers who show up every day on time are teachable, yet they will also go where the safety climate is better.
Implementing Tech as a Recruiting Tool
Since one of the biggest benefits of having a good safety program is that more people want to come work with you, it’s important to mention that staying up to date on technology can be another valuable recruiting tool. Millennials have grown up with technology, and individuals in construction, like any other field, are looking for jobs with the right tools and software in place. Business owners need to understand the importance of this.
“When you’re talking technology, it’s having things right at your fingertips,” Matheny comments. “You [are] able to have the tools that you need to be successful in operating a piece of equipment and performing an activity safely. What’s great about technology is they’re able to get a lot more information quickly.”
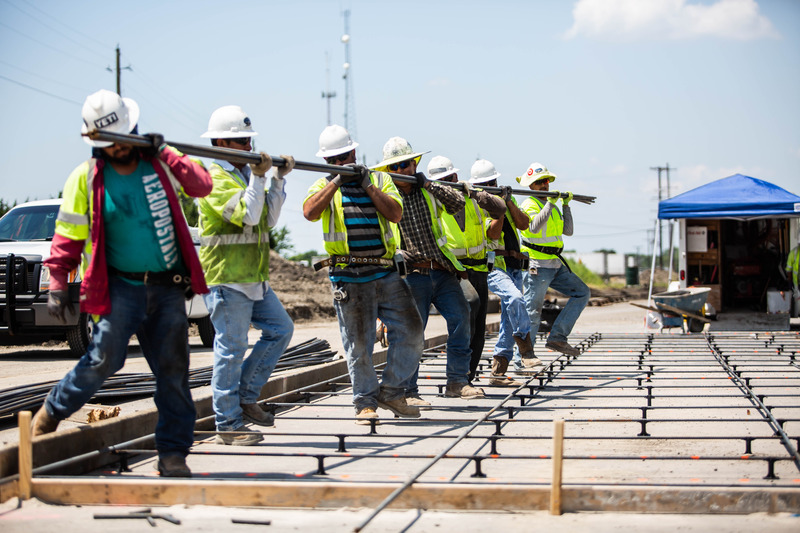
When HCSS speaks with contractors using the software, much of the feedback about the safety tool in particular, is loving the ability to provide training records instantly. There are no boxes and file cabinets to dig through or cluttered Excel spreadsheets lost on an old hard drive.
How to Calculate the ROI of a Safety Program
Adding up the ROI of a safety program, it’s not just avoiding the injuries, penalties, difficult time attracting talented workers, and even not being able to bid on certain opportunities because of a bad EMR – it’s also those production delays, which add up to detrimental lost time and labor on a jobsite. When that happens, it doesn’t take a genius to calculate the number of people standing around doing nothing but waiting and multiply that number by however long the investigation is going to take place. Everything adds up.
“It’s very difficult to get past safety compliance and into shifting your safety climate when you’re not utilizing technology,” Matheny states. “I personally just don’t know how you get there.”
Hope Matheny recalls the exact time she realized technology was needed in their organization. Following an OSHA inspection, they actually did pretty well but were still left with a couple of citations to discuss. Matheny wanted to advocate on behalf of their frontline supervisors and crew, but this meant she had to collect all of the necessary pieces of paper, including inspections, JSAs, and observations. For just that week alone, there were 3,000 pieces of paper she collected.
“That is really what caused me to shift my way of thinking, if there is a tremendous effort in compliance and we were not doing anything with it as an organization,” Matheny says. “When you put a dollar value on nearly 3,000 pieces of paper, just collecting them alone was expensive.”
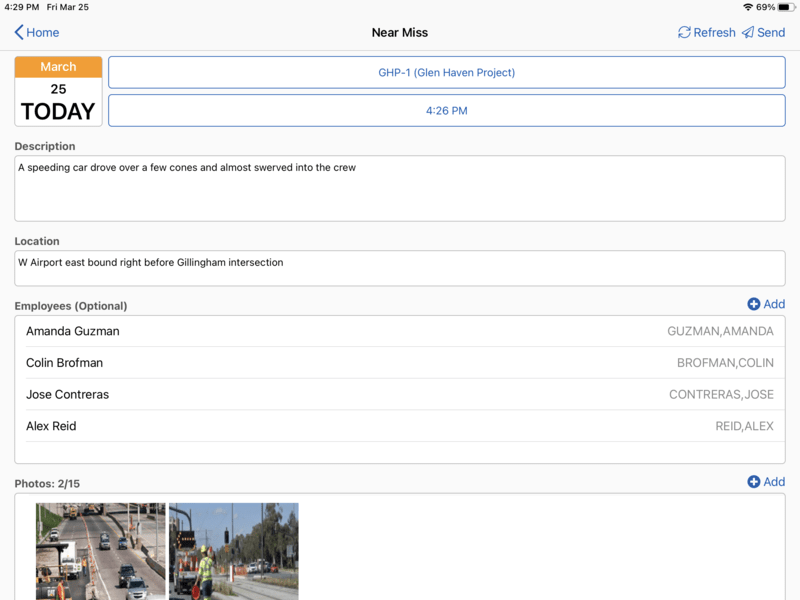
Additionally, clients are becoming much more in tune with what is being done to prevent risk. It’s not just the contractor’s reputation on the line – it’s theirs tool. When incidents occur, it’s not uncommon for a jobsite to be shut down for days to have interviews. They’re not going to let you start working until you have your full incident report and investigation completed and have verified your corrective action.
“Because of this heightened reputation that we’re up against as contractors, we are being shut down for days,” she adds. “[Even with a] small crew, and we’re talking two days, a hundred man hours that we just lost off of our schedule. It’s a big deal.”
Worse, when a team is behind schedule and under pressure, they’re often incentivized to cut corners and rush. This is when the rates of incidents are much higher. In fact, incidents are usually doubled during the rework phase. With technology software, it’s much easier to make sure that people are doing the required JSAs, meetings, and inspections so that crew members are constantly reminded they’re being held to a certain standard, as well as trained properly.
“It’s really hard to hold someone accountable to a value or a standard that they weren’t even aware of,” Matheny adds. “To even get to the accountability stage, you have to have good, consistent communication, and you have to have good training. That’s our responsibility.”
OSHA estimates contractors save between $4-6 or every $1 invested in an effective safety program. Overall, that’s because the processes that help prevent production delays involve having good organization and communication to ensure people know what’s happening at all times. This all begins with having a safety program firmly in place.
Take Control of Your Safety Program
HCSS works with 42 of the top 50 heavy civil contractors in the U.S. and helps onboard companies of all sizes, big or small, to benefit from HCSS Safety. Request more info to get started!
OSHA estimates that contractors save $4-6 for every $1 invested in an effective safety program.
Source: OSHA