Click to play video
Some of our 4,000+ customers
Improve equipment performance
Give your mechanics the entire work history on a tablet instead of chasing down a paper trail of equipment services.
Enhance operational efficiency
Don’t let fleet managers miss another preventive maintenance service. Automatically associate cost codes, part requests, documents, and checklists with PM services.
Make data-driven decisions
Provide real-time access to operational data across all departments by going paperless and having a full view of your fleet on a tablet.
Keep your fleet and profits healthy
Inspections
Automate your work orders after an inspection. No wasted time between identifying problems & fixing them.
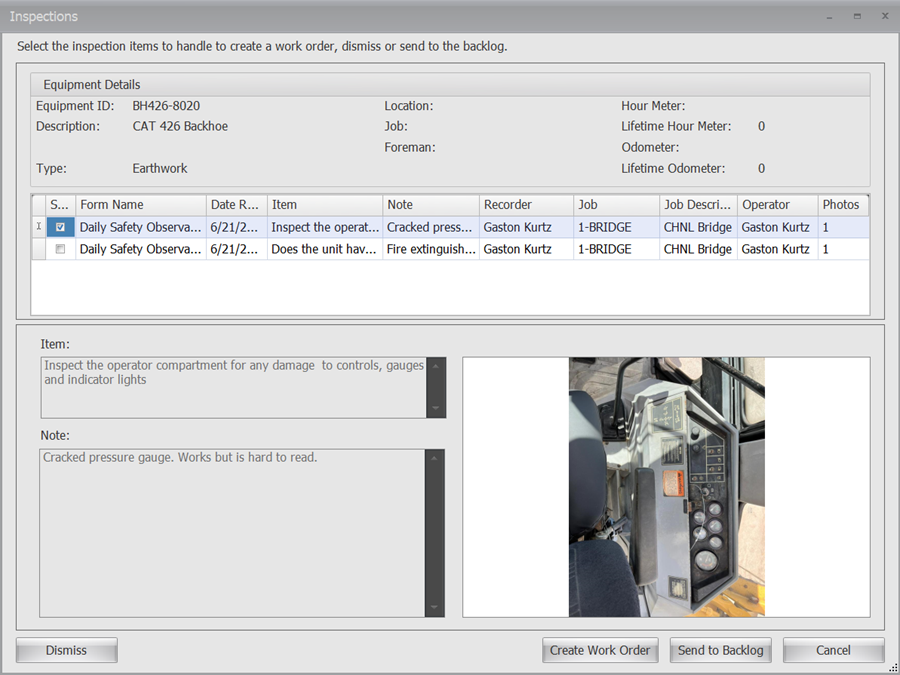
Preventive maintenance
Set automatic alerts for equipment certifications, work order due dates, inspections, and more.
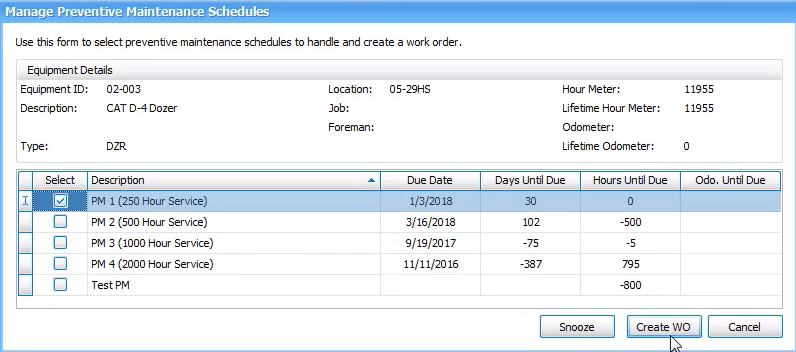
Work orders
Create detailed work orders to track equipment history, maintenance costs, and performance.
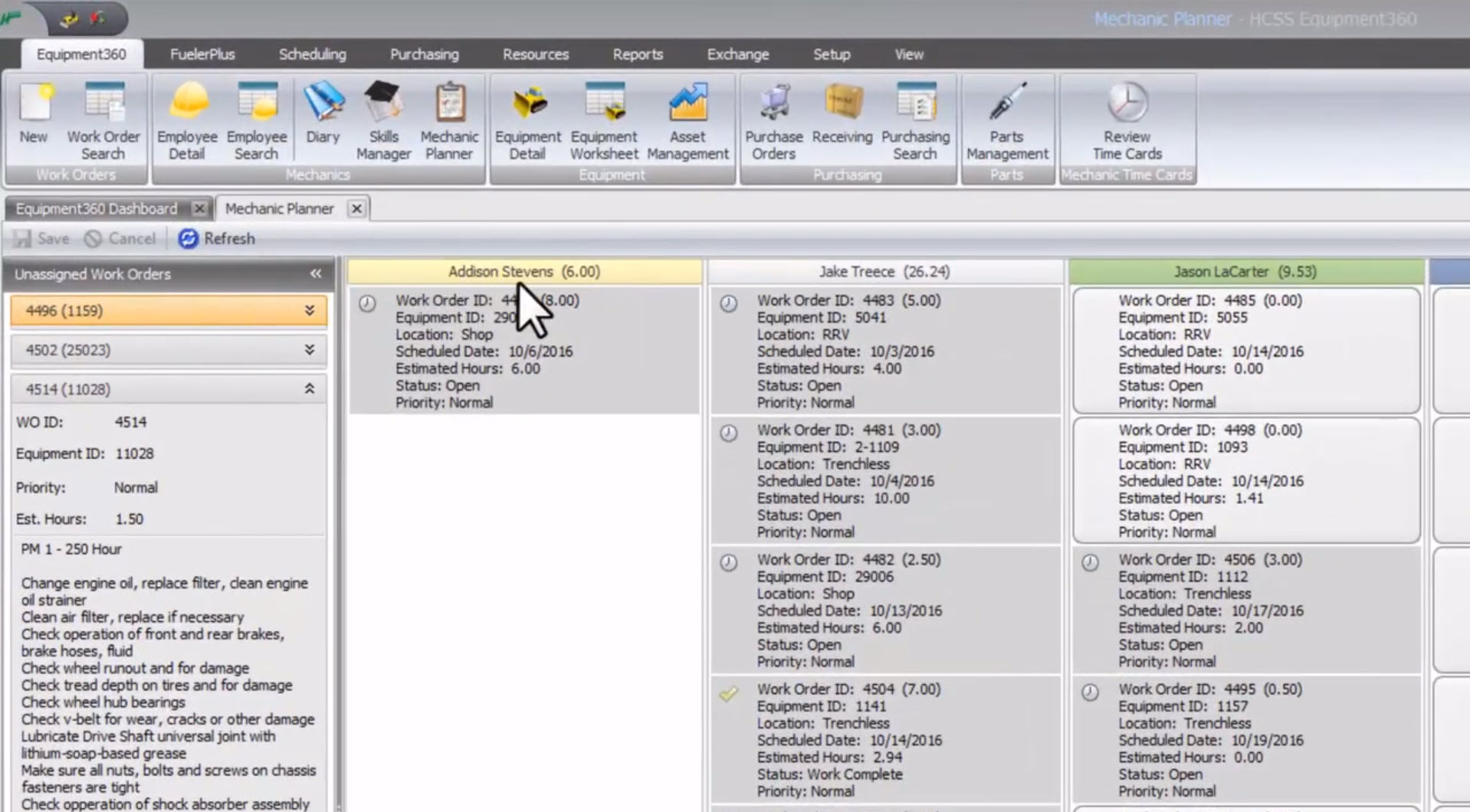
Inventory management
Track parts, purchases, and invoices. Set automatic alerts when it’s time to stock up.
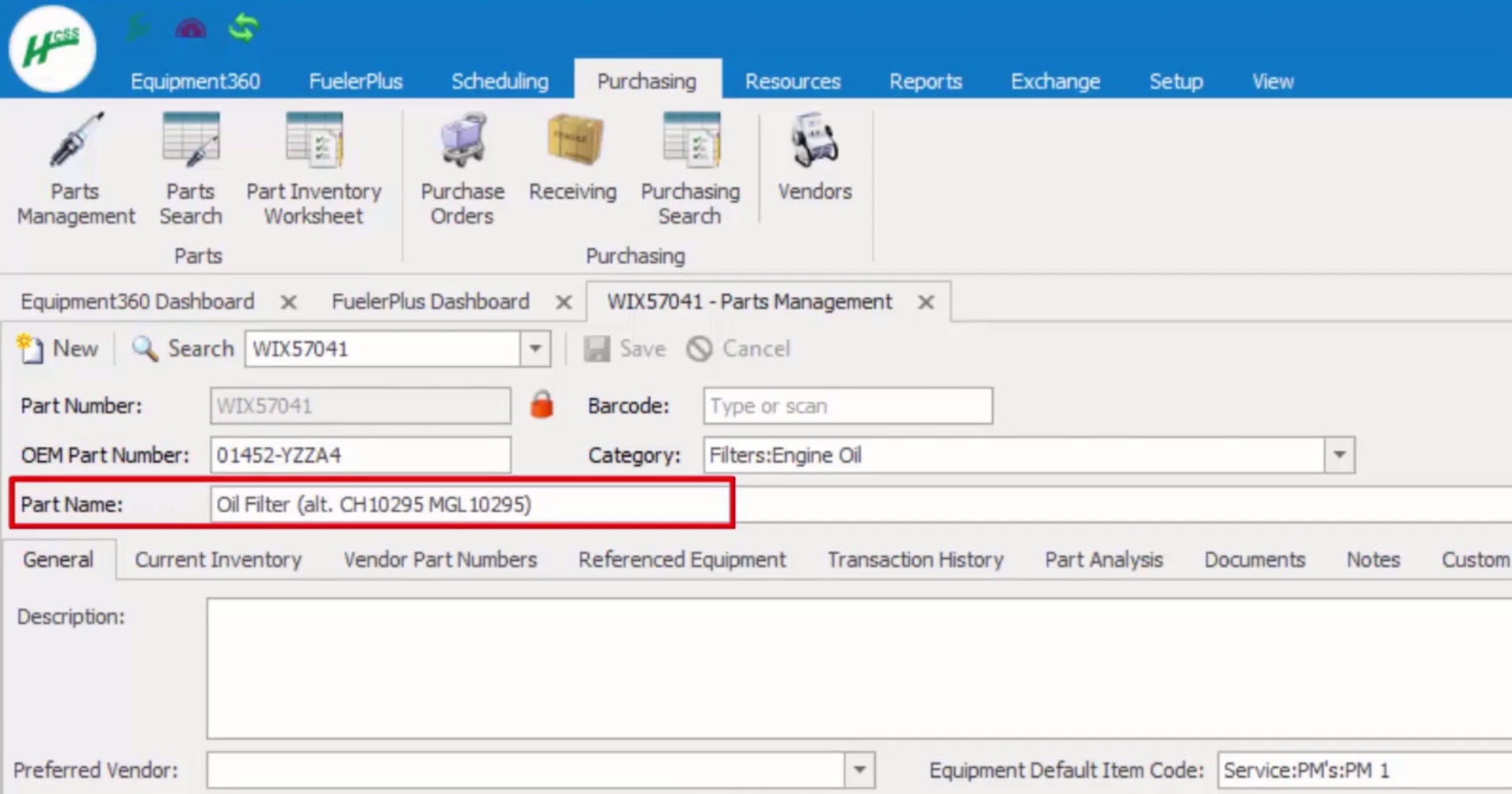
Maintenance requests
Put in repair orders straight from the field. Save time and reduce unexpected downtime.
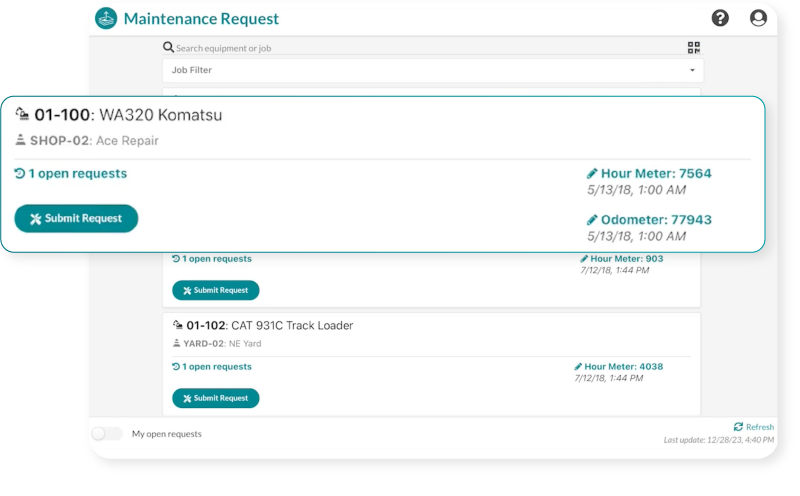
See why our customers trust Equipment360 to keep their fleet in tip-top shape
Click to play video
Rather than having this paper process, you have all the information in the tool and you can validate it using the tool.
- Ben Chung, MGE Underground
Click to play video
It’s important to HCSS that you’re successful with your implementation and experience with the product.
- Kenzie Clarkson, Sigfusson Northern LTD.
65%
fewer breakdowns for Equipment360 users
10%
reduction in repair work order cost
4.4/5
Apple App Store rating
Start managing your fleet in real-time and maximize profitability
Step 1
Share your business headaches
After submitting a demo request form, an HCSS expert will follow up with you by the end of the next business day to discuss your business needs and requirements.
Step 2
See HCSS in action
Then, we’ll walk you through a demo tailored to specific HCSS solutions that can help solve your current business problems.
Step 3
Get up and running in days
Finally, you’ll be assigned a dedicated implementation specialist who will manage your implementation from start to finish and ensure project completion.
Frequently asked questions
How does Equipment360 compare with other fleet management programs?
Most of our customers choose Equipment360 because it integrates with other HCSS software they own. A lot of companies manage their fleet with the equipment module that comes with their accounting software. They usually switch to Equipment360 because they need more features than what comes with the accounting software.
How does Equipment360’s Preventive Maintenance system work?
Equipment360 uses alerts to drive your Preventive Maintenance schedule. Preventive Maintenance alerts are based on three parameters: calendar days, runtime hours, and your equipment’s odometer.
What types of alerts can I set in Equipment360?
In Equipment360, you can track multiple types of maintenance alerts such as certification and licensing for your equipment, due dates for your work orders, field requests, preventative maintenance, reorder level for your inventory items, skills for your employees, and warranties for your equipment.
These alerts can easily be turned into work orders in three clicks.
How many Equipment360 licenses should I buy?
The number of Equipment360 licenses your organization should purchase depends on your company size and number of users. Your company’s license mix is customizable to suit your needs in the office and the jobsite.
Discover which license structure is right for you »
HCSS bases the suggested number of Equipment360 Manager licenses on the number of shop or fleet managers, executives, superintendents, project managers, accountants, and payroll managers that will be accessing Equipment360 at one time.
Equipment360 for the PC and laptop features shared licenses that can be used concurrently, so multiple users can be in the Manager system at one time. Companies typically start with one to two manager licenses unless they have more than $100 million in annual revenue, in which case they might consider one manager license for every two or three users.
Equipment360 Mechanic licenses for both laptop and mobile, as well as Mobile Mechanic licenses, are individually named per user. These licenses belong to the individual user and can travel from device to device by logging into the app.
Since mechanic licenses cannot be shared, you should purchase one license for each user accessing the Mechanic (or Mobile Mechanic) system.
Didn’t get all of your questions answered?
Request infoCurious if Equipment360 is the right fit for your business?
Chat with us to see the software in action!
Once you fill out the form, we’ll connect with you to answer your questions and help you decide if HCSS is the right software for you. Then, we’ll create a personalized demo tailored to your needs to show how Equipment360 can help solve your most pressing business problems around fleet management.